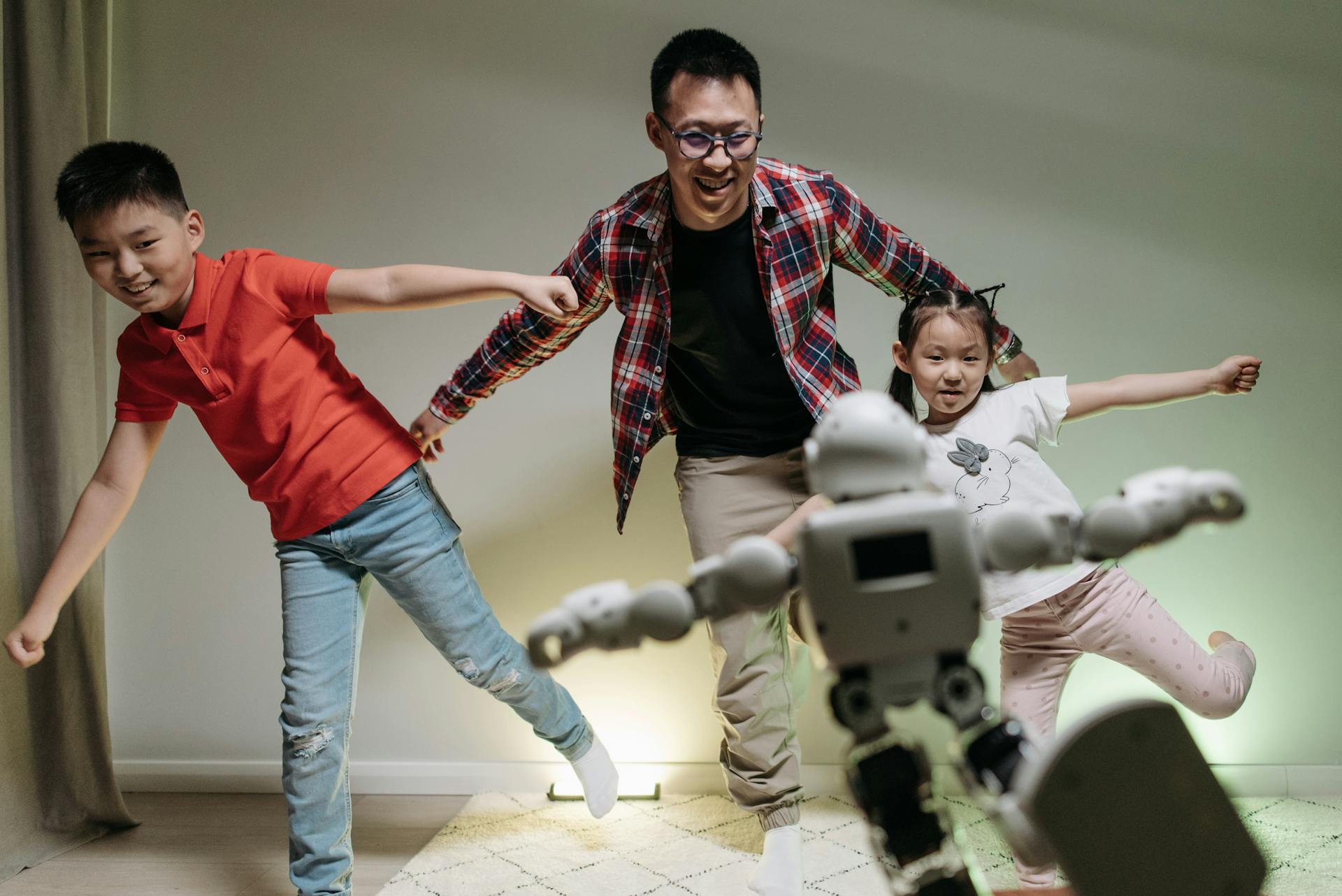
AI robotics is revolutionizing the way we think about automation and innovation. According to a recent study, the global AI robotics market is expected to reach $67.4 billion by 2025.
As AI robotics continues to advance, we can expect to see increased adoption in industries such as manufacturing, healthcare, and logistics. This is due in part to the ability of AI robots to perform tasks with precision and speed, reducing the risk of human error.
One of the key benefits of AI robotics is its ability to learn and adapt to new situations. This is made possible through machine learning algorithms, which enable AI robots to improve their performance over time.
Intriguing read: Artificially Intelligent Robots
Types of Locomotion
There are several types of locomotion in robotics, each with its own unique characteristics and advantages.
Legged locomotion consumes more power and requires more motors to accomplish a movement, but it's well-suited for rough and smooth terrain.
Wheeled locomotion, on the other hand, is more power-efficient and has fewer stability issues.
The complexity of legged robots lies in their legs, which need to be articulated well enough to provide stability and speed.
Here are some examples of different types of locomotion:
- Legged locomotion
- Wheeled locomotion
- Combination of legged and wheeled locomotion
- Tracked slip/skid
In legged locomotion, the total number of possible gaits depends on the number of legs. For a two-legged robot, there are 6 possible events, including lifting and releasing each leg separately or both legs together.
The number of possible events increases rapidly as the number of legs increases. For example, a six-legged robot has 39,916,800 possible events.
For more insights, see: Robot Learning
Components and Hardware
A robot's power supply can come from batteries, solar power, hydraulic, or pneumatic power sources. This is crucial for its overall functioning and efficiency.
The actuators in a robot convert energy into movement, making them a vital component. They work by converting the energy from the power supply into a physical motion.
Electric motors, whether AC or DC, are required for rotational movement in robots. This is essential for tasks that require precise and controlled movements.
Explore further: Energy-based Model
Pneumatic air muscles are another type of actuator that can contract almost 40% when air is sucked into them. This makes them suitable for applications that require a lot of force.
Muscle wires, on the other hand, contract by 5% when electric current is passed through them. They are a good option for applications that require precise and delicate movements.
Piezo motors and ultrasonic motors are also used in robots, particularly in industrial settings. They are known for their high precision and reliability.
Sensors are another critical component of a robot, providing real-time information about the task environment. They can take the form of vision sensors, which can compute depth in the environment, or tactile sensors, which mimic the mechanical properties of human fingertips.
Here's a list of the key components of a robot:
- Power supply (batteries, solar power, hydraulic, or pneumatic power sources)
- Actuators (convert energy into movement)
- Electric motors (AC/DC)
- Pneumatic air muscles
- Muscle wires
- Piezo motors and ultrasonic motors
- Sensors (vision, tactile, etc.)
For a computer vision system, the hardware requirements are similar to those of a robot. A power supply, image acquisition device (such as a camera), processor, software, display device, and accessories (like camera stands and cables) are all necessary.
In AI-powered robotics, the hardware can be categorized into computing hardware and robot hardware. Computing hardware can be general-purpose or specific-purpose, with the latter being more lightweight and cheaper.
Applications and Domains
AI robotics has numerous applications across various domains, including manufacturing, aerospace, disaster response, transportation, agriculture, healthcare, and customer service.
AI-powered robotic systems can be used for quality control, collaborative robots, autonomous robots, and assembly robots in manufacturing. They can also be used for autonomous rovers, robotic companions, and advanced drones in aerospace, disaster response, and transportation.
In healthcare, AI robotics can be applied to robotic assistants, robotic surgery, and service robots. In customer service, social robots and service robots can be used to provide assistance and support. Some specific examples of AI robotics applications include:
- Autonomous vehicles
- Face recognition
- Gesture analysis
- Robotic surgery
- Service robots
These applications and domains showcase the versatility and potential of AI robotics in various industries and fields.
Real-World Examples
In the field of agriculture, computer vision is used for tasks such as crop monitoring and yield prediction. This technology helps farmers make informed decisions about planting, harvesting, and crop management.
Agricultural drones equipped with computer vision can analyze crop health, detect pests and diseases, and even apply targeted fertilizers and pesticides. This can lead to increased crop yields and reduced environmental impact.
In the manufacturing industry, collaborative robots are being used to assist human workers with tasks such as assembly and packaging. These robots can work alongside humans, improving efficiency and reducing labor costs.
Autonomous robots are also being used in manufacturing to perform tasks such as quality control and material handling. They can operate around the clock, without breaks or fatigue.
The use of autonomous robots in manufacturing has improved production efficiency and reduced errors. They can also work in environments that are hazardous to human workers.
In the healthcare industry, robotic assistants are being used to assist medical professionals with tasks such as patient care and surgery. These robots can perform complex tasks with precision and accuracy.
Robotic surgery has also become increasingly common, allowing surgeons to perform operations with greater precision and reduced recovery time for patients. This technology has improved patient outcomes and reduced healthcare costs.
Here are some real-world examples of AI and robotics applications across various domains:
Data Collection
Data collection is a crucial step in developing AI robotics. The purpose, application area, and functionality of your robot will define the data scope it needs to train on.
For example, if your robot is meant to harvest crops, you'll need to train its computer vision model using a dataset of different crop images. This will enable the robot to distinguish between fruit and leaves, ripe and unripe fruit, and so on.
Data annotation and labeling are necessary for "raw" datasets. Online resources like ImageNet and CIFAR-10 offer annotated computer vision datasets, but if your application field is too niche, you may need to label your training data yourself using tools like Doccano, Prodigy, and Label Studio.
Data augmentation can be a lifesaver if your robot's environment lacks data that can be collected naturally. This involves increasing your existing dataset to help the system better handle unseen situations.
Dataset balancing is business-critical. If certain data categories are underrepresented, you risk making your model biased and erroneous.
You might enjoy: Ai and Ml in Data Analytics
Advances and Innovations
NVIDIA's advancements in AI and robotics are revolutionizing the industry. Demand for autonomous machines and AI-enabled robots is at an all-time high, with industries looking to improve operational efficiency and combat workforce shortages.
Developers are using NVIDIA Robotics full-stack, accelerated cloud-to-edge systems, acceleration libraries, and optimized AI models to develop, train, simulate, deploy, operate, and optimize their robot systems and software.
NVIDIA Research is focusing on areas such as robot manipulation, physics-based simulation, and robot perception, with the goal of developing the next generation of robots that can robustly manipulate the physical world and safely work alongside humans.
NVIDIA's Embodied AI group, GEAR, is developing a "foundation agent" for humanoids that can generalize across various skills and realities, unlocking autonomy for next-gen robotics. This technology has the potential to transform industries such as manufacturing, logistics, and healthcare.
For your interest: Artificial Intelligence Is the Theory and Development of Computer Systems
Autonomous Future
The autonomous future of robotics is an exciting and rapidly evolving field. Nvidia's Embodied AI group, GEAR, is developing a "foundation agent" for humanoids that can generalize across various skills and realities, unlocking autonomy for next-gen robotics.
Robotics is being used to solve real-world problems in various industries like manufacturing, logistics, and healthcare. AI is being used to enable breakthroughs in robotics that solve real-world problems.
One of the main challenges facing the integration of AI and robotics is the issue of job displacement. As robots become more likely to take over tasks that are done by people, some professions may become unnecessary and workers left without jobs.
However, it's worth noting that technological advancements also make new qualifications needed and occupations available. This is not a new phenomenon, as many past professions don't exist anymore.
To mitigate the risks associated with AI-powered robots, security best practices, policies, and strategies are being developed by the engineering community. This includes dealing with the potential for malicious actors to gain control over robotic systems.
In order to teach emotional intelligence to machines and enable robots to establish meaningful connections with people, researchers are working on finding a way to deal with unpredictable human behavior. This is a complex challenge that requires a multidisciplinary approach.
Consider reading: How Is Ai Used in Robotics
Advances Physical at CVPR with Largest Indoor Dataset
NVIDIA Advances Physical AI at CVPR with the Largest Indoor Synthetic Dataset.
Hundreds of teams from around the world tested their AI models on physically based datasets generated with NVIDIA Omniverse for the annual AI City Challenge at CVPR.
This massive undertaking helped researchers and developers advance the development of solutions for smart cities and industrial automation.
NVIDIA Omniverse is a powerful tool for generating synthetic data, which can be used to speed up AI development in various areas, including autonomous vehicles and robotic arms.
The results of this challenge will likely lead to breakthroughs in robotics that solve real-world problems in industries like manufacturing, logistics, and healthcare.
NVIDIA Research is focused on using artificial intelligence to enable these breakthroughs, with a goal of developing the next generation of robots that can robustly manipulate the physical world and safely work alongside humans.
The challenge was a significant step forward in the development of physically based simulation and synthetic data generation, which can accelerate development, testing, and validation of AI robots.
You might like: Ai and Ml Development Services
Frequently Asked Questions
Is the figure AI robot real?
Yes, Figure AI's humanoid robots are real, designed to perform physical tasks in complex environments. Developed by Figure AI, these AI-powered robots are a cutting-edge innovation in robotics.
Sources
- https://www.tutorialspoint.com/artificial_intelligence/artificial_intelligence_robotics.htm
- https://www.nvidia.com/en-us/industries/robotics/
- https://sciencehub.mit.edu/research/ai-robotics/
- https://builtin.com/artificial-intelligence/robotics-ai-companies
- https://waverleysoftware.com/blog/ai-in-robotics/
Featured Images: pexels.com